Introduction
A modern Warehouse Management System (WMS) is far more than inventory tracking—it’s the nerve center of your supply chain. But to unlock its full potential, your WMS must seamlessly connect with other enterprise applications. These integrations eliminate data silos, automate workflows, and ensure real-time visibility from order entry through final delivery. Below, we explore the must-have integrations for any robust WMS and explain how each one amplifies efficiency, accuracy, and customer satisfaction.
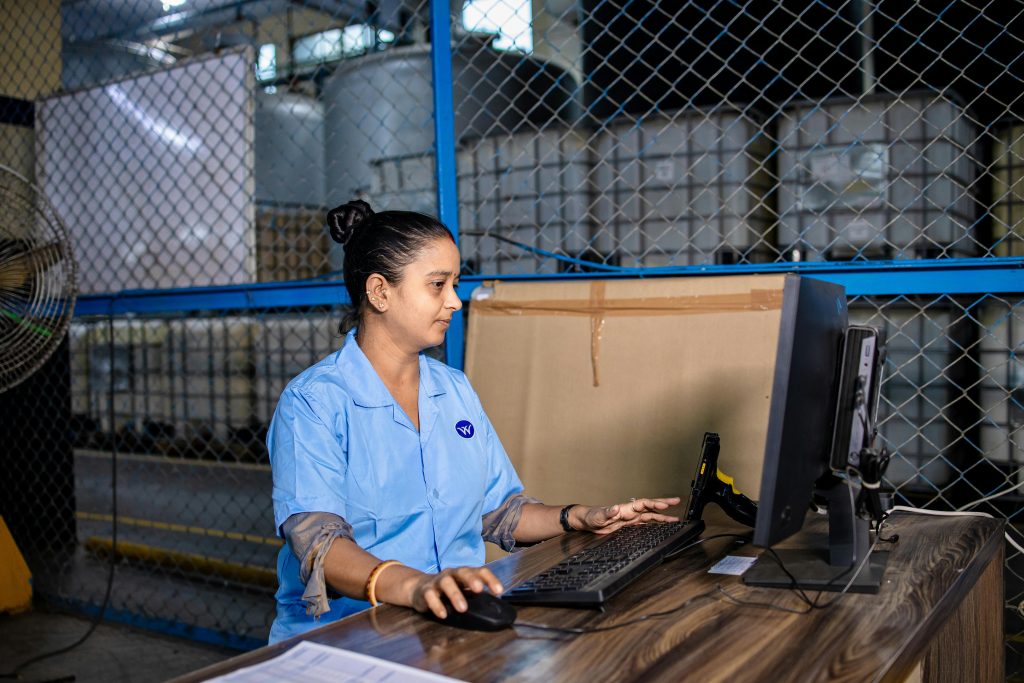
Enterprise Resource Planning (ERP)
Why it matters:
- Master data synchronization: Products, SKUs, units of measure, and locations update bi-directionally.
- Order flow automation: Sales orders created in the ERP flow directly into the WMS for picking and shipping.
- Financial reconciliation: Shipments, returns, and adjustments automatically feed back to cost and revenue modules.
Key capabilities:
- Near-real-time order/status updates
- Inventory levels reflected accurately in ERP dashboards
- Audit trails across both systems for compliance
Transportation Management System (TMS)
Why it matters:
- Carrier selection & rate shopping: Enables your WMS to pass shipment dimensions and weights to the TMS for optimized routing.
- Load planning: Ensures pallets and cartons are grouped to maximize truck utilization.
- Visibility & tracking: TMS delivers delivery ETAs and tracking milestones back to the WMS for customer notifications.
Key capabilities:
- Automated tendering of shipments to carriers
- Real-time freight cost calculation
- Exception alerts for delays or re-routing
E-Commerce Platforms & Marketplaces
(Shopify, Magento, Amazon Marketplace, etc.)
Why it matters:
- Order ingestion: Online orders sync instantly with the WMS to kick off picking, packing, and shipping.
- Inventory updates: Stock changes reflect back to your storefront to prevent oversells.
- Returns processing: RMA data flows into the WMS for quick inspection and restocking.
Key capabilities:
- Webhooks or APIs for order/event notifications
- SKU mapping and bundle handling
- Automated back-order or preorder management
Electronic Data Interchange (EDI) & B2B Portals
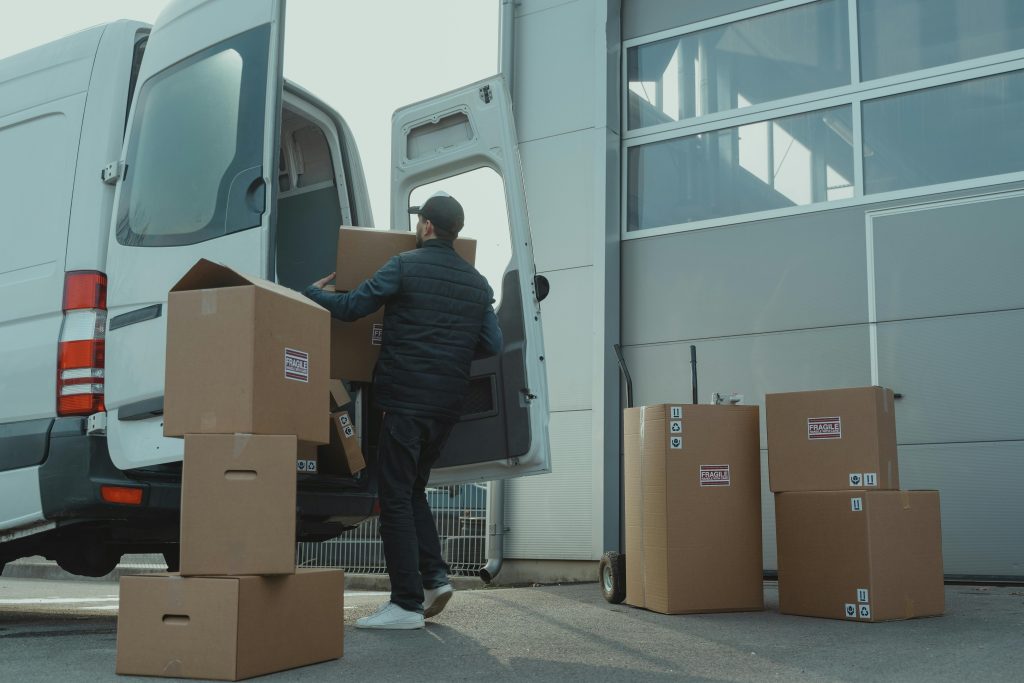
Why it matters:
- Standardized documents: Invoices, ASN (Advanced Shipping Notices), purchase orders, and shipping notices use EDI to minimize manual entry.
- Retail compliance: Many large retailers mandate EDI for order fulfillment and invoicing.
- Speed & accuracy: Automated EDI transactions reduce errors and accelerate cash-to-cash cycles.
Key capabilities:
- Support for ANSI X12, EDIFACT, or industry-specific subsets
- Acknowledgment and error-handling workflows
- Integration with trading-partner directories
Yard Management System (YMS)
Why it matters:
- Dock scheduling: Coordinates inbound and outbound dock appointments to prevent congestion.
- Trailer tracking: Monitors trailer status and location on your yard.
- Harmonized workflows: YMS feeds dock-ready and load-ready signals to the WMS for seamless handoffs.
Key capabilities:
- Real-time gate check-in/check-out data
- Push/pull integration of yard events and WMS task priorities
- Automated detention and demurrage tracking
Material Handling & Automation Controls
(Robots, conveyor systems, sorters)
Why it matters:
- Task orchestration: WMS issues pick-to-light, put-to-light, or conveyor transport commands directly to automation controllers.
- Throughput optimization: Dynamic slotting recommendations adjust storage locations based on pick frequency.
- Error reduction: Barcode scans and weight checks mesh with robotics to catch mis-picks instantly.
Key capabilities:
- OPC/UA or proprietary PLC interfaces
- Real-time machine-status feedback to the WMS dashboard
- Automated exception alerts for jams or equipment faults
Business Intelligence (BI) & Analytics Platforms
(Tableau, Power BI, Looker)
Why it matters:
- Data consolidation: Warehouse KPIs—throughput, labor productivity, order accuracy—feed your enterprise data warehouse.
- Advanced analytics: AI/ML-driven forecasts for labor planning, inventory replenishment, and slotting optimization.
- Self-service reporting: Empower stakeholders with dashboards and ad-hoc querying.
Key capabilities:
- OData, SQL, or API-based connectors for ETL
- Pre-built WMS KPI templates and data models
- Row-level security to protect sensitive data
Customer Relationship Management (CRM)
(Salesforce, Dynamics 365)
Why it matters:
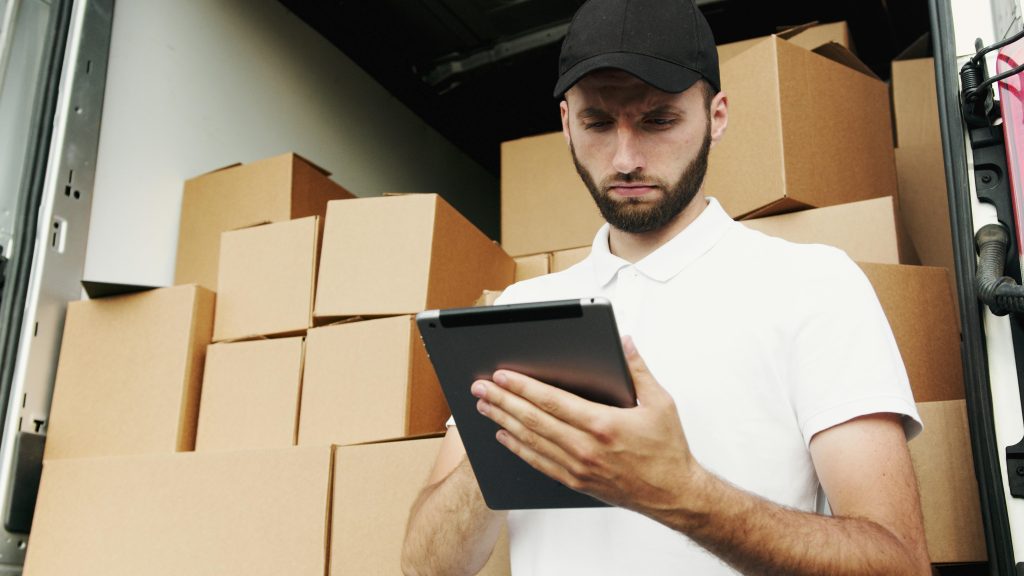
- Order status visibility: Customer-facing teams can check shipping ETAs and exceptions without logging into the WMS.
- Returns and warranty: Seamless ticket creation in CRM when RMA data arrives from the WMS.
- Upsell and cross-sell: Leverage fulfillment data to recommend accessories or reorders.
Key capabilities:
- Real-time case and order look-ups
- Automated case creation for shipping delays or discrepancies
- Customer satisfaction surveys triggered post-delivery
API-First & Microservices Architecture
Why it matters:
- Flexibility: Rapidly add new channels, carriers, or automation devices without monolithic upgrades.
- Scalability: Spin up integration services independently to handle peak loads (e.g., holiday e-commerce surges).
- Maintainability: Decouple modules for faster development and lower downtime.
Key capabilities:
- RESTful or gRPC endpoints for each integration
- Event-driven architecture with message queues (Kafka, RabbitMQ)
- SDKs and developer portals for secure partner onboarding
Conclusion
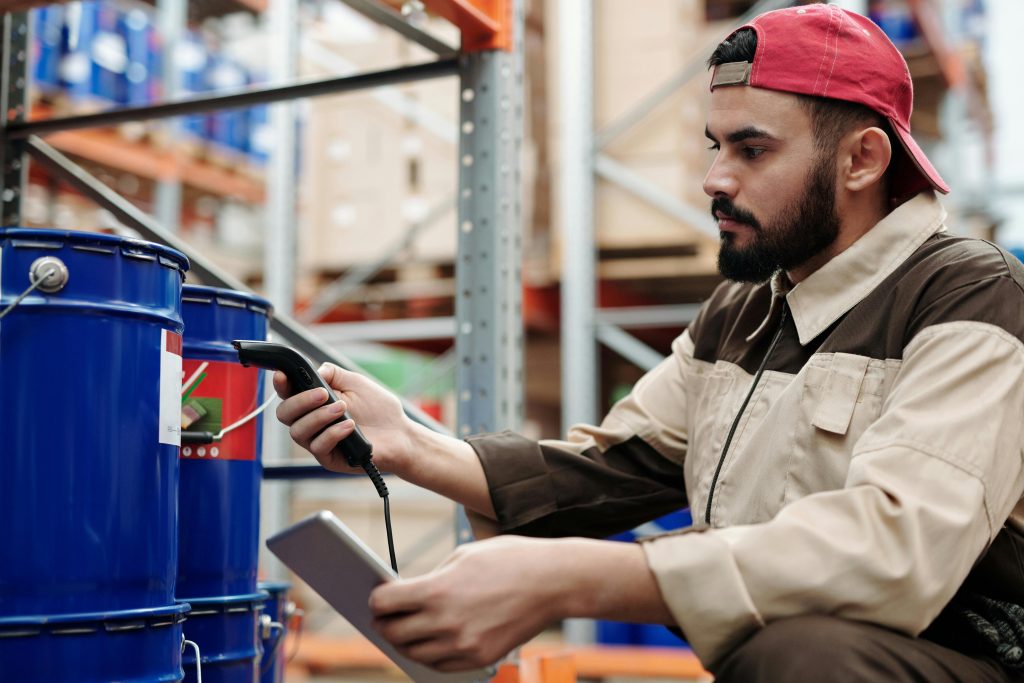
A best-in-class WMS isn’t an island—it thrives when integrated across your technological ecosystem. By linking your WMS with ERP, TMS, e-commerce platforms, EDI, YMS, automation controllers, BI tools, CRM, and embracing an API-first architecture, you create a seamless, data-driven supply chain. These integrations minimize manual effort, reduce errors, accelerate order fulfillment, and provide actionable insights—from warehouse floor to C-suite dashboards. When selecting or upgrading your WMS, ensure it offers robust, pre-built connectors and a flexible integration framework to support both your current needs and future growth.