Introduction
Efficiently managing inbound trailers is the backbone of a high-performance distribution center. When trailers arrive on a chaotic, first-come–first-served basis, docks clog up, labor sits idle, and throughput grinds to a halt. Yard Management Systems (YMS) bring order to the madness—scheduling appointments, orchestrating gate check-ins, tracking every trailer’s location, and sequencing dock pulls with precision. In this post, we’ll dive deep into how yard management coordinates inbound trailers at each stage of the process, share real-world analogies to simplify complex workflows, and offer expert tips to squeeze every ounce of efficiency from your yard. Whether you’re a supply-chain veteran or just exploring YMS capabilities, you’ll come away with actionable strategies to minimize dwell time, maximize asset utilization, and keep your warehouse humming like a well-tuned engine.
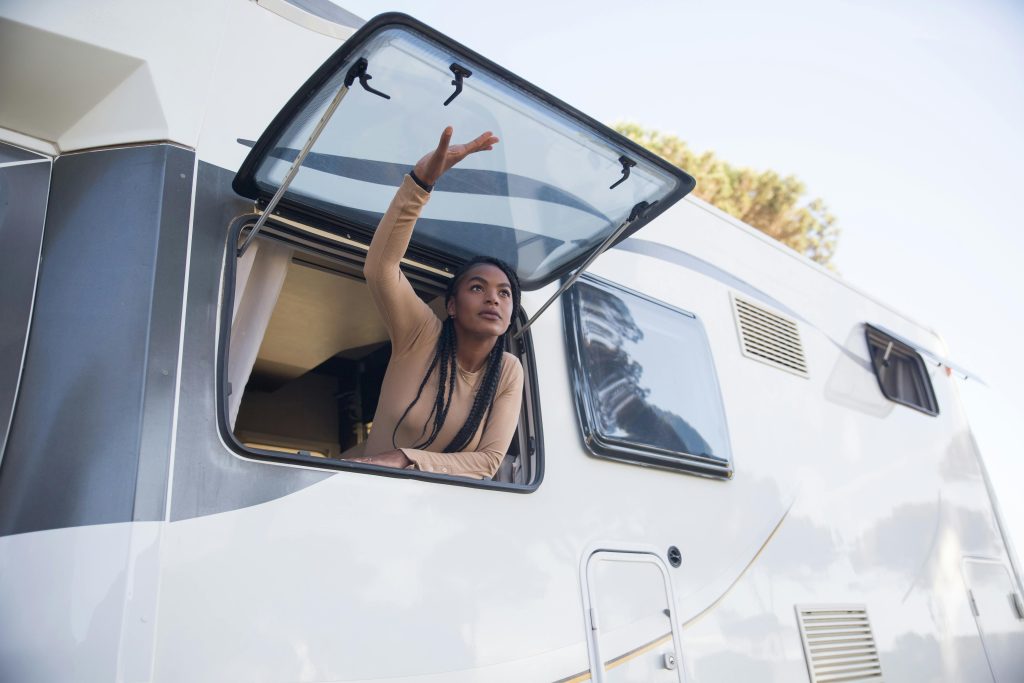
1. Understanding Yard Management and Inbound Trailers
1.1 What Is Yard Management?
A Yard Management System is a software platform that:
- Schedules and tracks trailers as they enter and exit the yard
- Manages dock door assignments to optimize unload/load sequences
- Provides real-time visibility into trailer status and location
- Generates analytics on dwell times, labor efficiency, and yard utilization
1.2 Why Focus on Inbound Trailers?
Inbound trailers carry the raw materials and products that fuel your fulfillment and assembly lines. Poorly coordinated arrivals lead to:
- Yard congestion, as trailers stack up waiting for access
- Dock idleness, when no trailer is available to unload
- Labor inefficiencies, with jockey drivers and dock hands standing by
- Increased detention fees, if carriers wait too long
Analogy: Think of your yard like an airport apron. Just as air traffic control schedules arriving flights, assigns gates, and coordinates ground crews, your YMS orchestrates trailer traffic, dock doors, and yard jockeys.
2. Appointment Scheduling & Pre-Arrival Planning
2.1 Carrier Appointment Booking
- Self-Service Portals & EDI: Carriers book time slots through an online portal or via Electronic Data Interchange, selecting windows based on trailer type, load requirements, and special instructions.
- Capacity Rules & Validation: The YMS enforces rules—e.g., no more than five refrigerated trailers per hour—and validates key data such as weight, temperature control, and required lift-gate service.
2.2 Assigning Yard Slots & Dock Windows
- Staging Slot Reservation: Once an appointment is confirmed, the system reserves a nearby yard slot for pre-staging.
- Dock Appointment Assignment: Based on the facility’s schedule and load priority, the YMS assigns a dock-door window for unloading, ensuring balanced utilization across all doors.
Expert Insight: Implement dynamic slotting, where high-priority loads (e.g., perishable goods) receive prime slots, while low-priority shipments wait in overflow zones.
3. Gate Check-In & Yard Entry
3.1 Gatehouse Validation
- Appointment Verification: Gate attendants scan a barcode or enter the trailer ID to confirm the appointment window.
- Document Inspection: The YMS checks bills of lading, PO numbers, and compliance documents (weight certificates, HAZMAT paperwork).
- Initial Condition Report: Any visible damage, seal breaks, or cleanliness issues are logged before the trailer enters the yard.
3.2 Yard Stall Assignment
- Automated Slot Allocation: The system selects a specific stall based on proximity to the assigned dock, trailer size, and compatibility with other staged trailers.
- Interactive Yard Map: Gate personnel and jockeys reference a color-coded map on handheld devices, instantly locating the correct parking spot.
Real-Life Example: A national retailer reduced gate wait times by 30% after switching to barcode-based check-ins tied to their YMS.
4. Real-Time Visibility & Tracking
4.1 Mobile Scanning & IoT Integration
- Handheld Scanners: Yard jockeys scan trailer IDs at each move—checking in, staging, pulling to dock, and releasing.
- RFID & GPS Tags: For high-volume yards, active RFID or GPS on trailers provides continuous location updates without manual scans.

4.2 Status Updates & Alerts
Each trailer carries a dynamic status tag:
- Checked In
- Staged
- Pending Unload
- Unloading
- Unloaded / Reload Ready
- Released
The YMS can trigger notifications for:
- Missed appointments (e.g., trailer not at dock within its window)
- Overstays (e.g., trailer parked too long in staging)
- Temperature excursions for refrigerated loads.
Pro Tip: Integrate your WMS (Warehouse Management System) and TMS (Transportation Management System) for end-to-end visibility—from shipper to final dock door.
5. Dock Door Sequencing & Pull-Ahead
5.1 Load-Ready Queues
- Pre-Unload Readiness: The YMS identifies which staged trailers have cleared paperwork, reached the door area, and are fully loaded/temperature stable.
- Order Prioritization: Based on product velocity, customer SLAs, and labor availability, the system ranks trailers in a queue.
5.2 Dynamic Sequencing Algorithms
- Shortest Processing Time (SPT): Prioritize trailers with the smallest unload expected time to maximize throughput.
- First-In, First-Out (FIFO): For perishable goods, ensure the earliest-arrived trailers unload first.
- Mixed-Model Sequencing: Combine rules—e.g., high-priority, high-volume SKUs first, followed by smaller loads.
5.3 Pull Plan Dispatching
- Driver Instructions: Jockey drivers receive turn-by-turn instructions on mobile devices—“Move Trailer T405 to Dock 7 in 5 minutes.”
- Buffer Windows: Allow a small window before and after each dock window to absorb minor delays without cascading disruptions.
Analogy: Just like air traffic controllers coordinate runway clearances to avoid runway incursions, your YMS sequences trailers to prevent yard “traffic jams.”
6. Unloading, Turnaround & Release
6.1 Pre-Positioning & Unloading
- Staging Near the Door: Thirty minutes before the dock appointment, the YMS triggers a “pull-ahead” so the trailer is waiting at the door.
- Dock Assignment Confirmation: Dock hands confirm the trailer ID via a handheld scan before starting unload.
6.2 Turn Time Monitoring
- Start/End Scans: Scanning at the start and end of unload captures the actual dock time versus planned time.
- Performance Dashboards: Real-time KPIs such as average unloading duration, door utilization rates, and bottleneck alerts help supervisors reallocate labor on the fly.
6.3 Post-Unload Decisions
- Empty Trailer Handling: Send empties to a designated “reload” zone or back to the carrier, based on load plans.
- Reload Scheduling: If the trailer is to be reloaded, assign a reload window and staging slot in the same YMS.
- Release & Gate-Out: Final paperwork is confirmed and the trailer is released back through the gatehouse, closing the loop.
Expert Insight: Setting target unload times for each door (e.g., 60 minutes per dry-load trailer, 90 minutes per refrigerated load) provides clear goals and drives continuous improvement.
7. Best Practices & Expert Tips
7.1 Maintain Accurate Master Data
- Trailer Attributes: Length, height, weight capacity, refrigeration, hazmat certifications
- Dock Profiles: Which doors can handle what trailer types and load sizes
7.2 Regularly Audit Yard Layout
- Flow Analysis: Confirm that staging zones and dock proximities match traffic patterns.
- Yard Slot Rebalancing: Reassign high-traffic stalls to accommodate seasonality (e.g., holiday peak vs. slow season).
7.3 Continuous Improvement Cycles
- Root Cause Analysis: When dwell times spike, trace back through gate logs, staging records, and unload scans to pinpoint chokepoints.
- Kaizen Events: Host cross-functional teams—operations, safety, IT—to workshop process tweaks every quarter.
7.4 Integration & Automation Roadmap
- IoT Expansion: Pilot smart yard sensors for hot-spot monitoring (e.g., temperature, trailer fullness).
- Machine Learning Sequencing: Leverage predictive models to forecast yard congestion and proactively adjust schedules.
- Carrier Collaboration: Share yard data with carriers via APIs so they can optimize outbound runs based on your staging status.
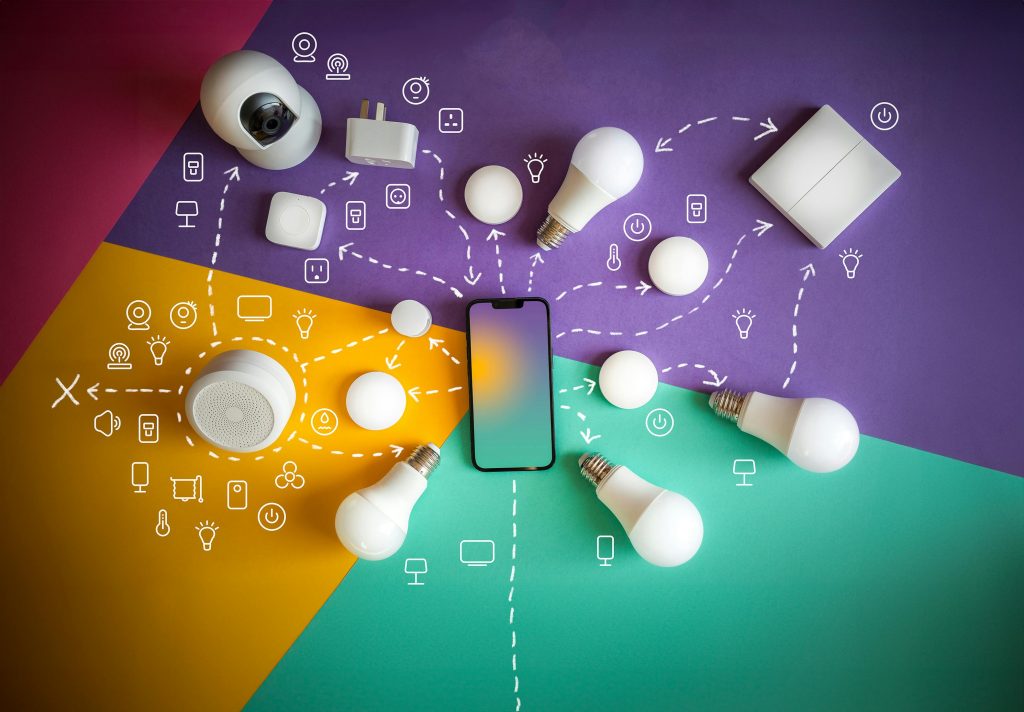
Real-World ROI: One Fortune 500 retailer cut average trailer dwell time from 36 hours to 10 hours within six months of implementing advanced YMS sequencing and real-time alerts.
Conclusion
Coordinating inbound trailers through a modern Yard Management System transforms your yard from a congested holding pen into a finely choreographed extension of your warehouse. By enforcing appointment windows, automating gate check-ins, maintaining live visibility, and sequencing dock pulls with intelligent algorithms, you’ll slash dwell times, boost labor productivity, and fortify carrier relationships. Start by mapping your current processes, then incrementally adopt these best practices—your operational resilience and bottom-line savings will thank you.